As a secondary or tertiary crushing machine, the cone crusher is widely applied in mining, metallurgy, construction, and road building industries, valued for its high stability, strong capacity, and excellent reduction ratio. However, its performance and efficiency heavily rely on the quality and maintenance of various accessories.
The main accessories in cone crushers include: the moving cone, fixed cone, liners (mantle and concave), eccentric bushing, main shaft, transmission shaft, upper and lower frames, adjustment ring, spring or hydraulic system, and lubrication components. Though these are not the primary structure of the machine, they directly influence operational efficiency, durability, and maintenance costs.
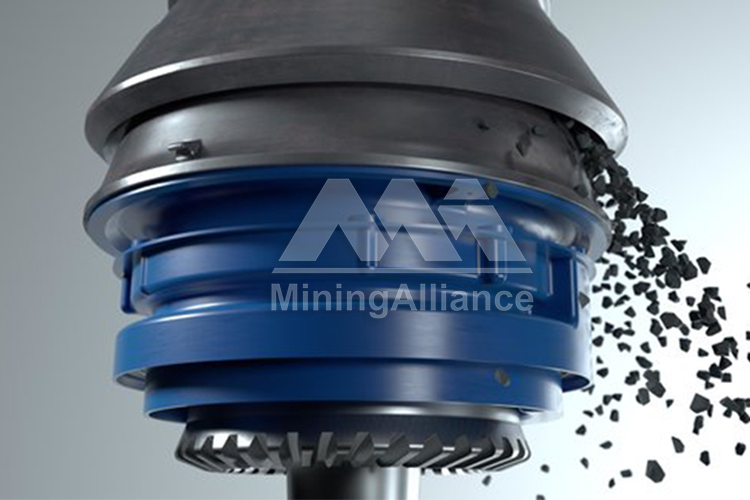
Liners (mantle and concave) are the most wear-prone components, typically made of high manganese steel or composite wear-resistant materials. Their hardness and toughness affect crushing capacity and final product shape. Timely replacement of worn liners ensures uniform output size and protects the main machine from overload.
The eccentric bushing and main shaft are vital parts of the drive system. Poor lubrication or worn bearings may cause abnormal vibrations, unstable discharge, or even shaft breakage. Regular inspection of clearances and lubrication conditions is essential to stable performance.
The adjustment ring and locking system control the discharge opening size, directly affecting the particle size of finished products. Any wear or loosening here can lead to inconsistent discharge and reduced product quality.
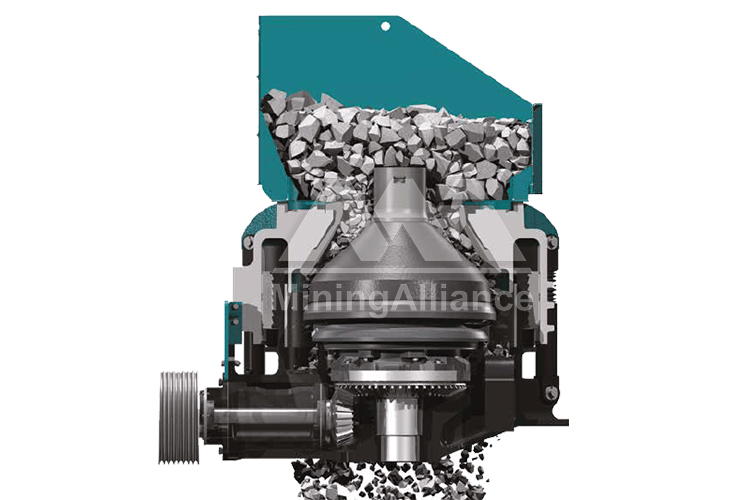
The lubrication system plays a critical role as well. Proper lubrication reduces wear and extends the lifespan of key components such as the shaft and bearings. It’s recommended to change the lubricant regularly and clean the oil circuit to prevent failure caused by contaminants.
In summary, the efficient operation of a cone crusher depends on the coordinated performance and maintenance of its accessories. Using genuine quality parts and implementing a scientific maintenance schedule not only prolongs equipment lifespan but also minimizes operational costs and maximizes productivity.