Jaw crushers, as one of the most common primary crushing equipment, have their parts' selection and maintenance directly affecting operational efficiency and lifespan. Key components include jaw plates (moving and fixed), side plates, toggle plates, eccentric shaft, and bearings.
First, jaw plates are among the most critical consumables in a crusher, responsible for material fragmentation. Choosing the right jaw plate material, such as high manganese steel or chrome-molybdenum alloy, is crucial because these materials offer excellent wear resistance and toughness. Regular replacement of worn jaw plates prevents a decline in crushing efficiency and addresses safety issues during operation.
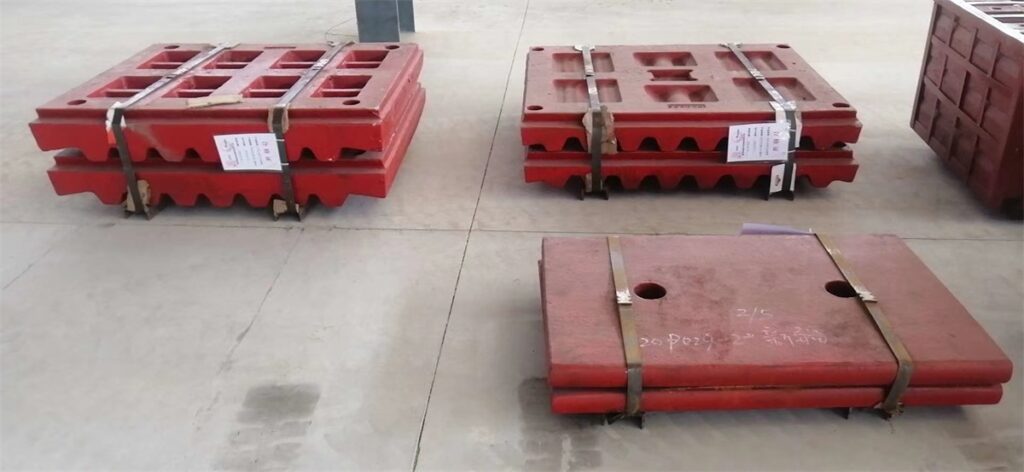
Side plates and toggle plates play vital roles in protecting the main structure and absorbing shock forces. Side plates protect the sidewalls of the crusher from material impact, while the toggle plate breaks under overload conditions to protect more expensive components.
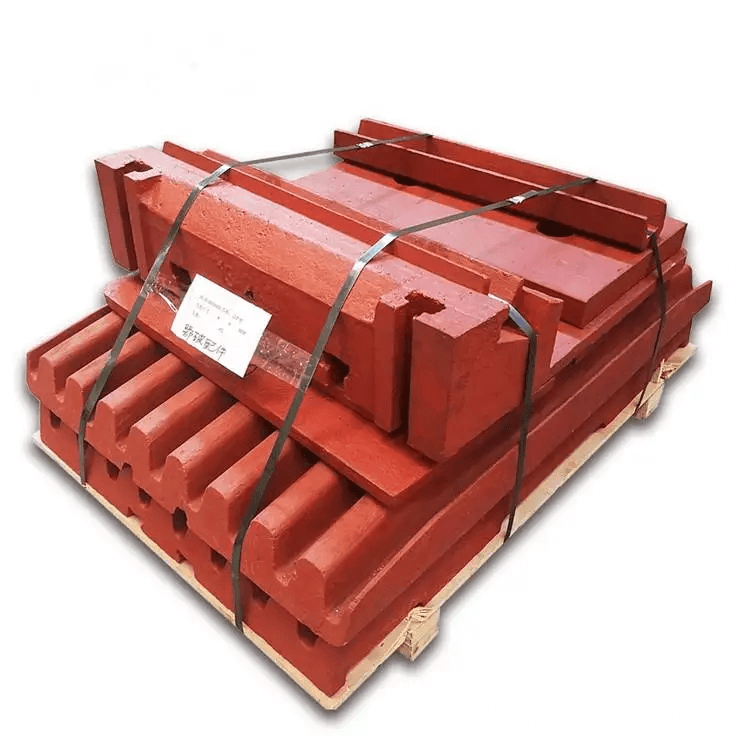
The eccentric shaft is the core driving component of the crusher, responsible for the oscillation of the moving jaw. Selecting high-quality, wear-resistant materials for the eccentric shaft and regularly checking for wear is a crucial step in maintaining smooth operation.
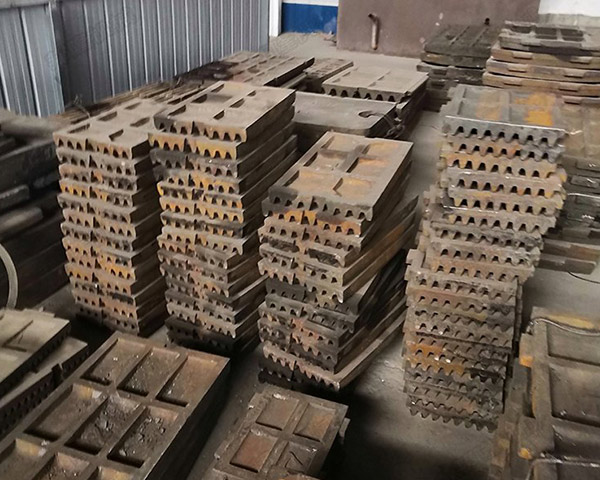
Bearings are essential for crusher performance, bearing all operational loads. Using high-quality bearings can extend the life of the equipment while reducing maintenance costs.
In terms of maintenance, regularly inspecting all parts for wear, lubricating bearings on time, and ensuring all connections are tight. With a good maintenance plan, the service life of a jaw crusher can be significantly extended, improving production efficiency.