The selection of materials for jaw crusher parts significantly affects their performance, cost, and lifespan. The choice of material for different components must consider the stresses they endure, wear conditions, and the chemical environment.
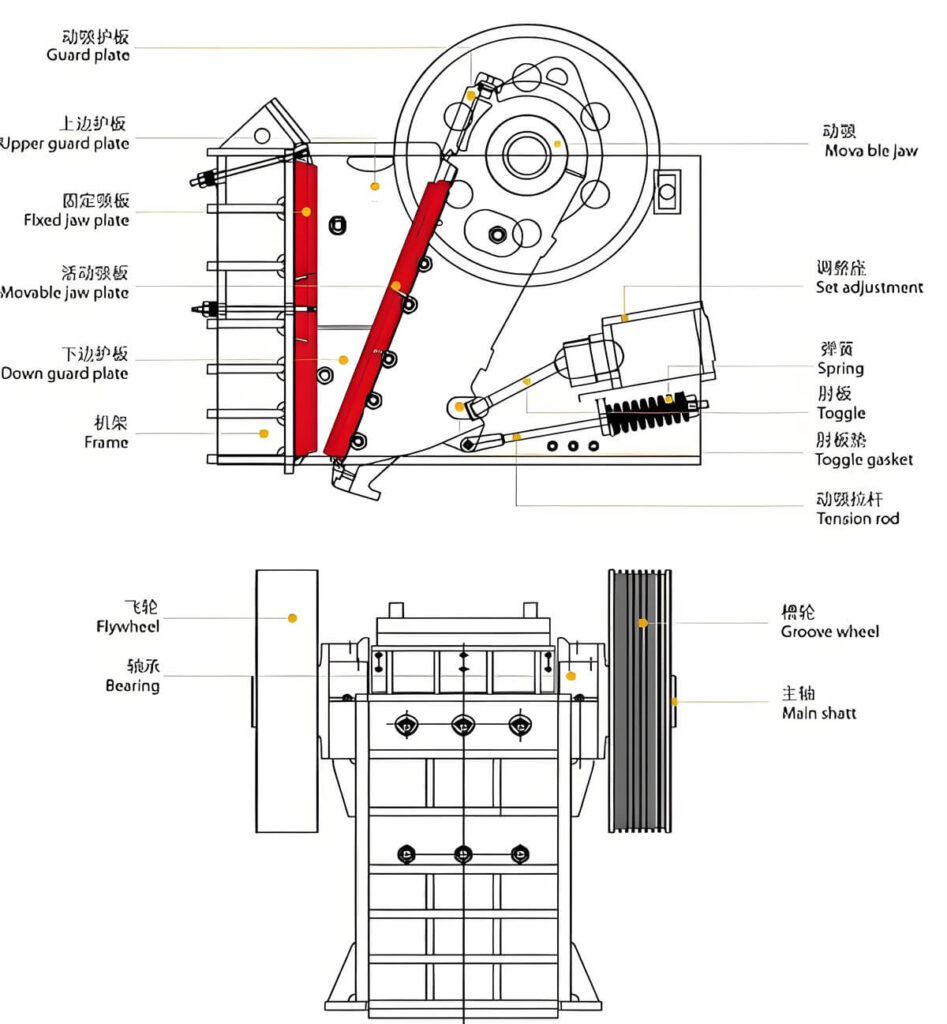
Jaw plates are typically made from high manganese steel (Mn13 or Mn18), which hardens under impact and wear. In recent years, composite materials like chrome-molybdenum alloys and high-chrome cast iron have been adopted, providing better wear resistance and corrosion resistance under various crushing conditions.
Toggle plates and side plates are often made from low alloy steel or cast iron, emphasizing toughness and impact absorption. Some manufacturers also use composite materials or add special alloys to enhance the performance of these parts.
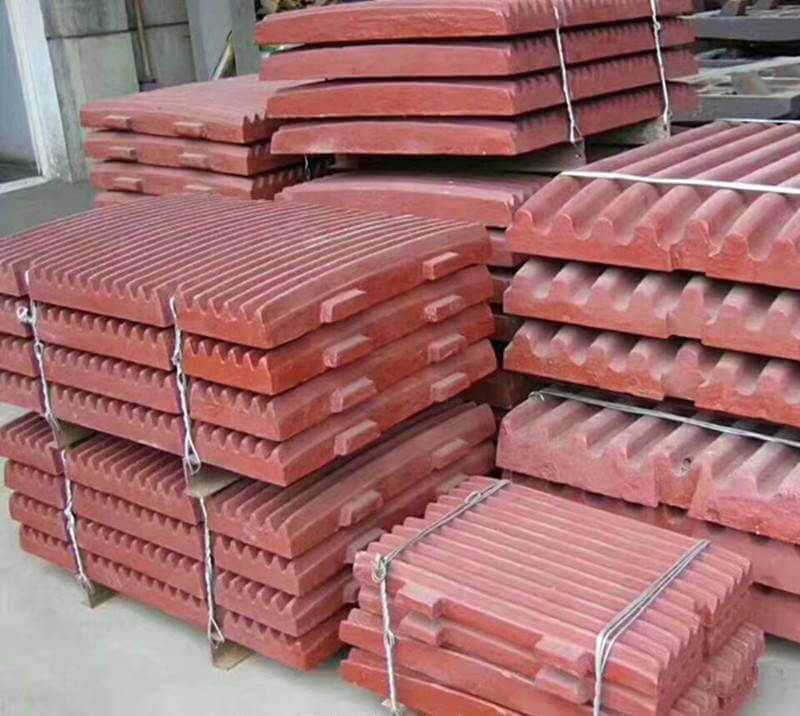
The eccentric shaft is generally made from alloy steel, heat-treated to increase strength and wear resistance. Choosing the right heat treatment process not only extends the shaft's life but also reduces the risk of fracture during operation.
Bearings are usually made from high-carbon chromium steel, although ceramic or specially coated bearings might be used in some applications to handle extreme conditions.
For performance optimization, the design and manufacturing process of the parts are also crucial. For example, the tooth profile design of jaw plates affects crushing efficiency; a well-designed tooth profile can reduce material dwell time in the crushing chamber. Surface treatment techniques, such as hardening or coating, can further enhance part wear resistance.
By selecting appropriate materials and optimizing design, jaw crusher parts can significantly improve the overall performance of the equipment, reduce operational costs, and extend service life.