Breakthrough in Wear-Resistant Materials Extends Service Life of Cone Crusher Parts
Recently, a well-known domestic mining equipment manufacturer announced the launch of a new generation of cone crusher wear parts. Utilizing advanced alloy materials and heat treatment processes, these parts significantly improve wear resistance and impact resistance. It is reported that the service life of these new wear parts in hard rock crushing operations has increased by more than 30% compared to traditional parts, effectively reducing equipment downtime and replacement frequency, thereby saving substantial maintenance costs for mining companies.
Intelligent Monitoring System Launched for Real-Time Wear Alerts
To further enhance the operational efficiency of cone crushers, the manufacturer has integrated an intelligent wear monitoring system into the new generation of parts. By collecting real-time wear data through sensors and combining it with big data analysis, the system can provide early warnings for part replacement, preventing equipment failures caused by excessive wear. This innovative technology not only improves equipment reliability but also offers scientific support for production planning in mining enterprises.
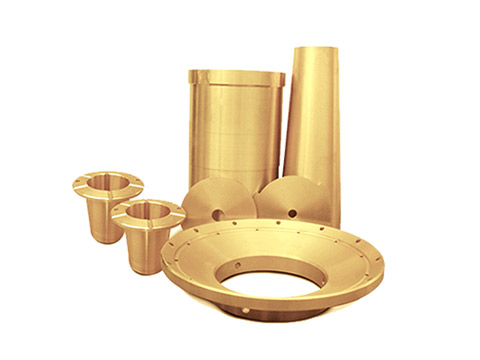
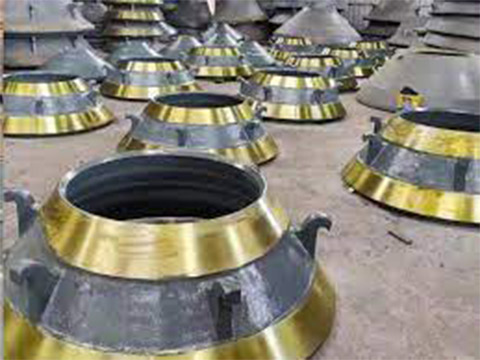
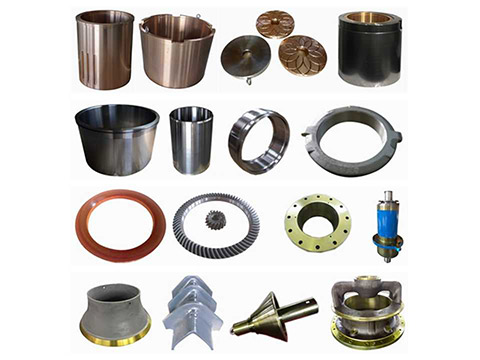
Eco-Friendly Design Promotes Green Mining
Notably, the new generation of cone crusher parts incorporates eco-friendly design principles. By optimizing the structure of the parts, dust generation during the crushing process is reduced, and recyclable materials are used in manufacturing, minimizing resource waste. This initiative aligns closely with the concept of green mining and has garnered widespread attention within the industry.